Autonomous soil sampling boat
- CategoryClass project
- Project dateSpring 2023
- Skills usedDesign, manufacturing, CAD
About this project
For 2.017, Design of Electromechanical Robotic Systems, we were asked to build something that would help researchers study harmful algal blooms. Harmful algal blooms, or HABs, occur when colonies of algae grow out of control and produce toxic or harmful effects on their environment. These blooms are becoming increasingly widespread and severe due to climate change, which improves conditions for their growth. There are many types of HABs, but since we're located in Massachusetts, we decided to focus on Alexandrium catenella, a major HAB-forming dinoflagellate found in northeast and northwest coastal regions. In New England, Alexandrium catenella is of great concern because it produces saxitoxin, the neurotoxin behind Paralytic Shellfish Poisoning (PSP). When contaminated seafood is consumed, PSP can lead to sickness, paralysis, and even death.
Some types of harmful algal blooms, including Alexandrium catenella, have a particular stage of their lifecycle called cysts, where the algae go dormant to protect itself until more favorable conditions arise. However, what causes cysts to bloom is poorly understood, as collecting samples is difficult and expensive. After consulting with experts and discussing our learning objectives, we determined that one useful niche where we would be able to assist is soil sampling. We decided to create a boat that could autonomously collect soil samples to help overcome this sampling bottleneck. By collecting more data, we can create better predictive models that can better inform policymakers and aquafarmers so they can pull their shellfish out of the water before HABs arrive.
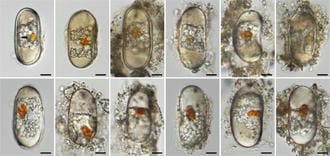
I worked on the mechanical design of the catamaran platform, working closely with the sampling team to ensure integration.
We selected a catamaran base to provide stability to our platform. To simplify the design for our short timeline, we used premade plastic hulls and added a custom framing of 80/20 T-slots and aluminum tubing for structural support and easy mounting points. For stationkeeping, we have four T200 thrusters at 45-degree angles. To traverse between waypoints, we are using two T500 thrusters (which are stronger than the T200s) in a differential thrust configuration. A sheet of marine-grade plywood is attached to the top of the catamaran to mount all other systems.
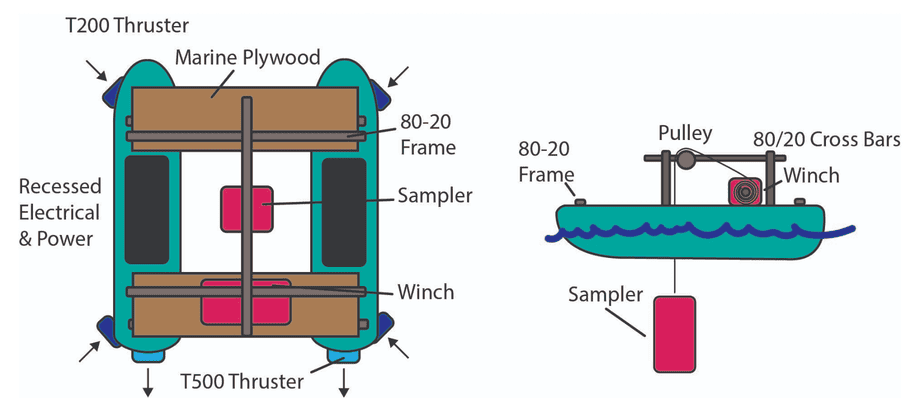
In order to connect the aluminum tubing and thrusters to the 80/20 base, we used 3D-printed carbon-fiber
composite using a Markforged printer.
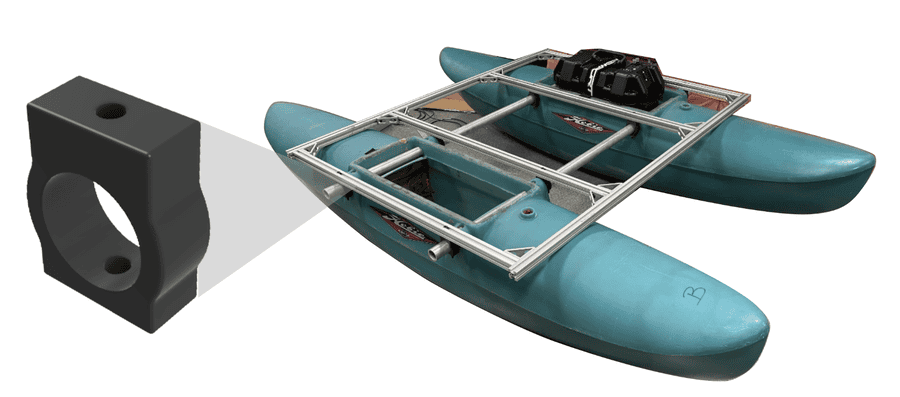
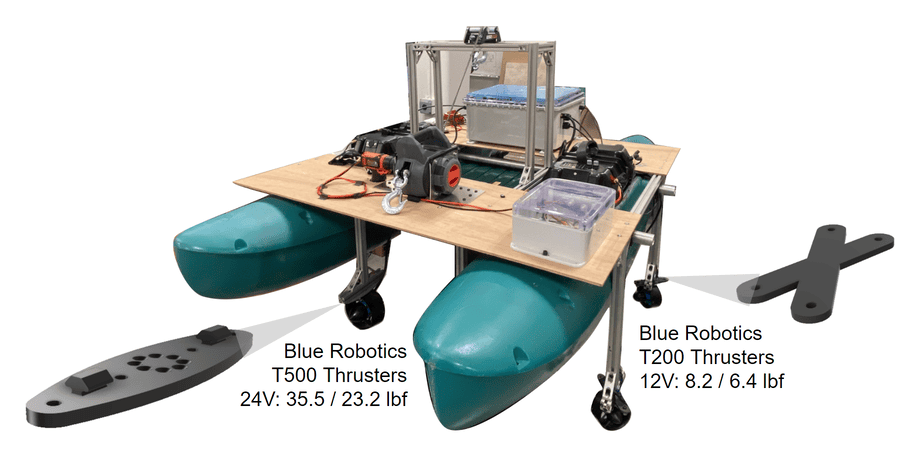
To lift and deploy the sediment sampler, we needed to create a winch and support system.
To do this, we used a winch designed to move vehicles and modified a drill connected to our
electrical system. The rope of the winch goes over a large pulley and moves the sampler up
and down. A frame for the sampler was connected to the chassis frame and houses the sampler
when it isn't deployed.
Early on in the design process, the team decided to make the sampler a passive system because running a cable to provide power would increase the likelihood of entanglement. After some research, we chose to make a spring-loaded multicore system that preserves the water-mud interface. Our solution is comprised of an outer frame that moves down with the inner portion of the sampler; once the outer frame makes contact with the sea floor, it remains stationary as the inner portion continues to move down. The difference in height as the inner portion moves relative to the now stationary outer frames releases a pin that closes the sediment sampler.
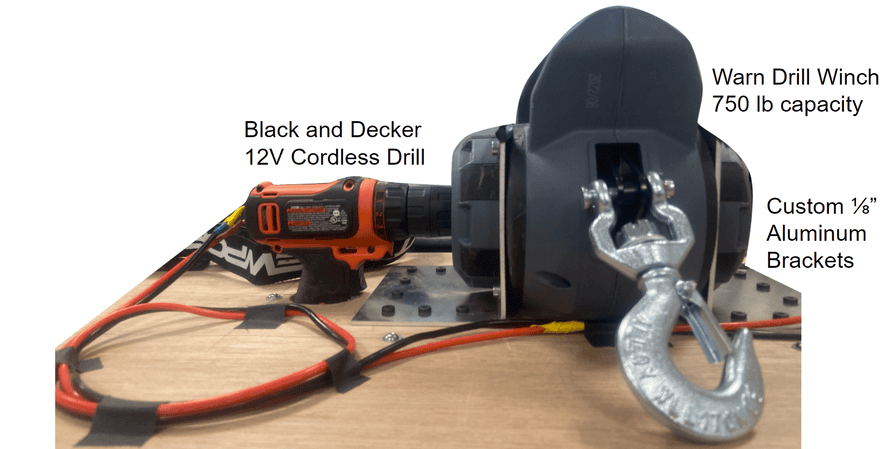
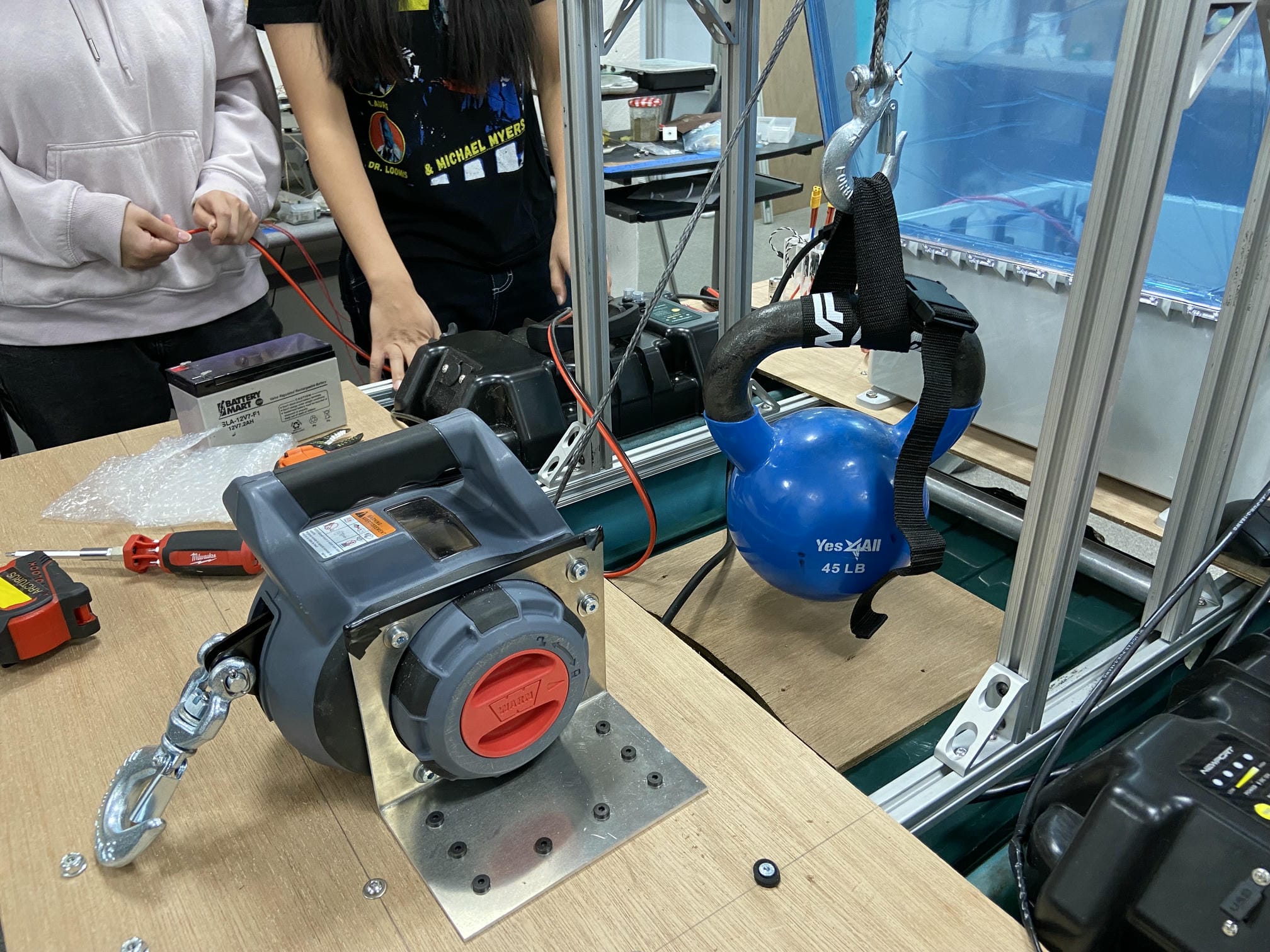
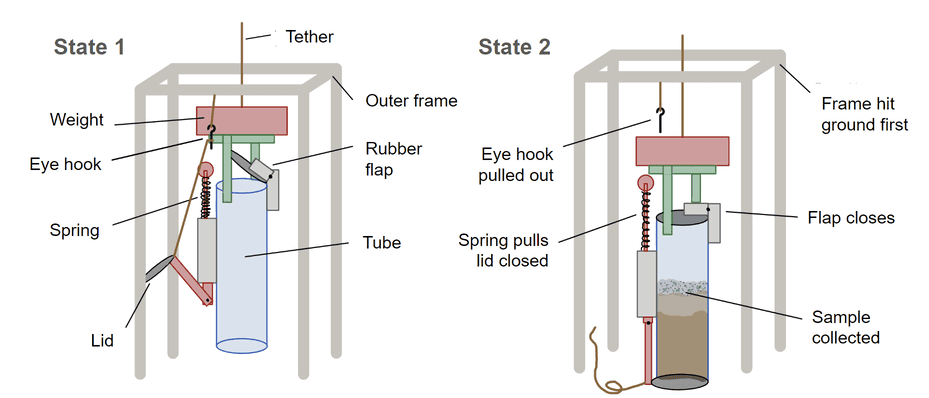
Here is are videos of the winch system lowering the sampler down and the sampler deploying after contacting.
The goal for the electronics was to provide power management and control to the rest of the system. We utilized two 12V AGM batteries to power all systems on the boat. A Raspberry Pi controlled the stationkeeping and main navigation thrusters as well as the deployment of the sediment sampler. At a high level, it followed the following wiring diagram.
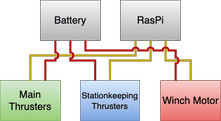
For a more detailed look at our wiring, please refer to our complete wiring diagram.
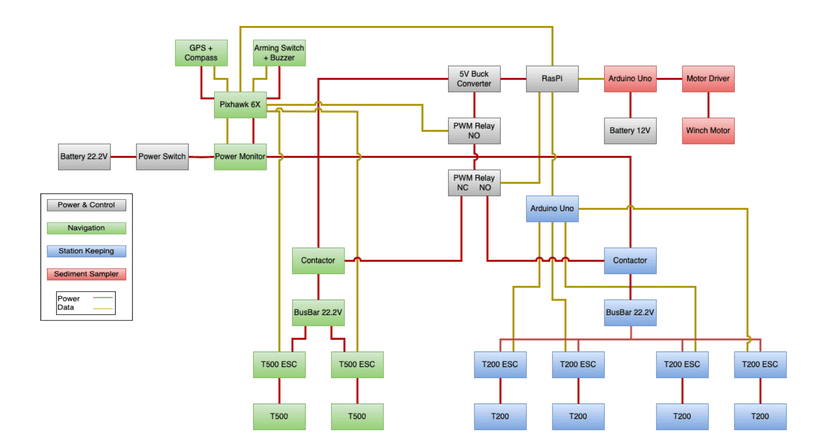
Altogether, the completed platform looked like this!
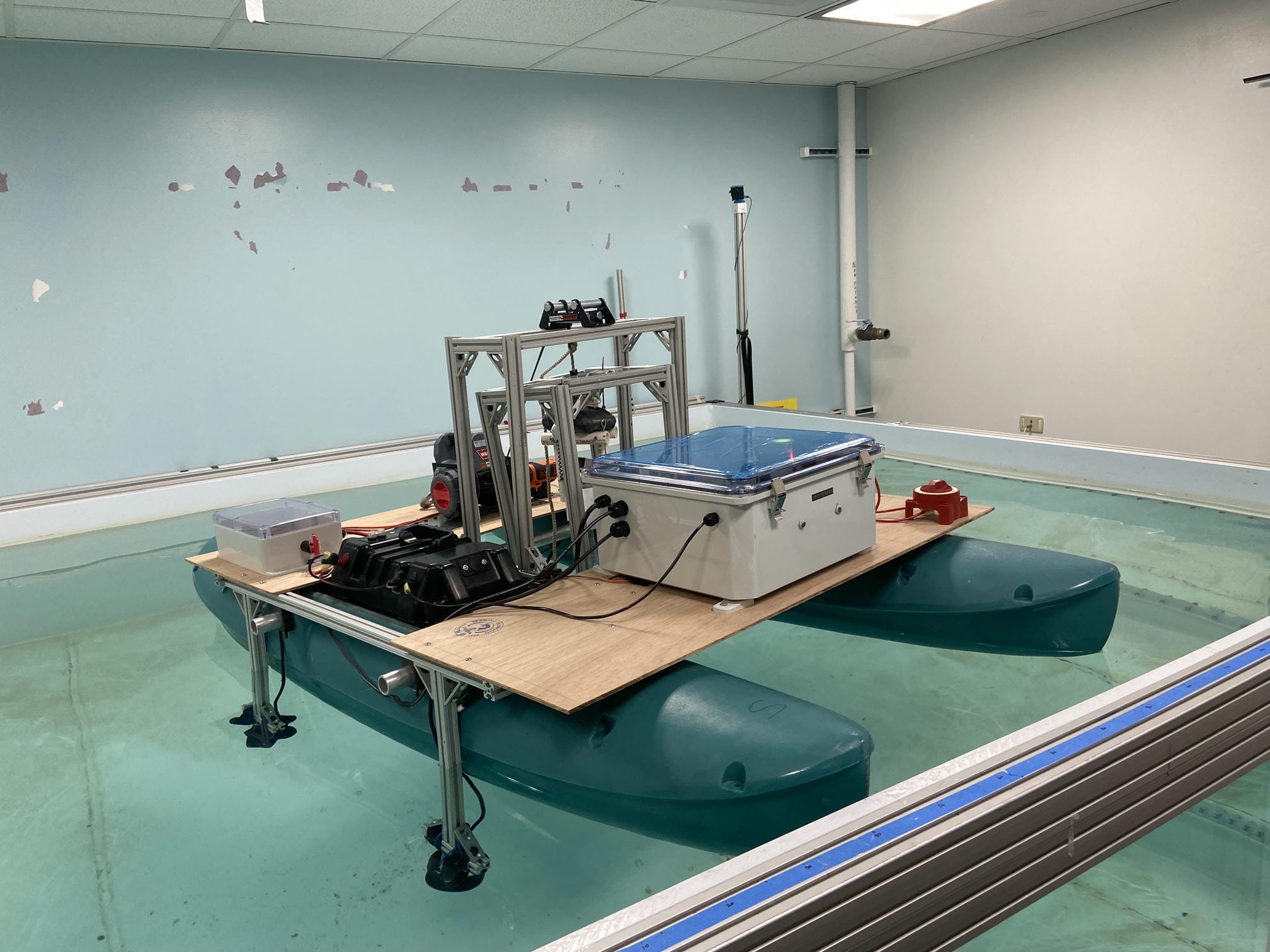
On the software end, we implemented some very simple stationkeeping (refer to the diagram for our control scheme),
but there is potential for further development of waypoint navigation using GNSS and even collision avoidance with
the addition of sensors (perhaps a stereoscopic depth camera or LiDAR). It would also be useful to detect obstacles on the bottom
of the ocean floor using a fish-finder sonar to ensure the catamaran is actually able to collect a sample in a given location.
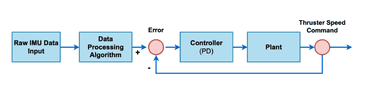
To learn more about the entire system overall, as well as our overall design process, please read our final presentation and our final report.
In our final test in the Charles River, we demonstrated RC control of our vehicle and remote raising and lowering of our sampler. This validated our design as a proof-of-concept that might be further developed for higher sampling robustness, increased sampling capacity, and higher-level autonomy.