Dino tissue box
- CategoryFor fun
- Project dateJanuary 2023
- Skills usedWoodworking, veneering, Adobe Illustrator, laser cutting, miter saw, CNC router
About this project
This project was my first time working with veneer and doing traditional woodworking! I thought it would be cute to create a custom tissue box using some scrap around a makerspace.
First, I traced a screenshot of the Google dinosaur game in Illustrator to create the shapes I wanted to cut out.
Typically veneer cutting is done using a technique called double bevel marquetry, in which a knife cuts two layers of veneer at once. Because of the geometry of the layout, the piece of veneer on the bottom fits perfectly into the space left behind by the top piece, with incredible tolerances.
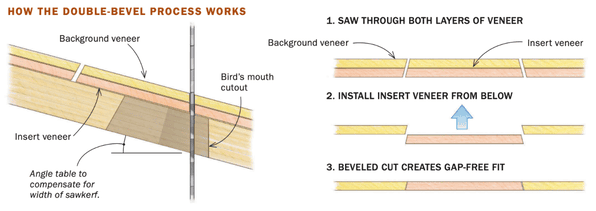
Unfortunately, I didn’t have access to one of these machines, so I had to laser cut my veneer. The kerf loss during the lasering process was minimal though, so I didn’t mind.
After laser cutting my veneer, I mixed and matched the different shades of wood to maximize contrast on each side. I then glued the veneer onto plywood squares and then vacuum formed them to ensure good contact and constant pressure.
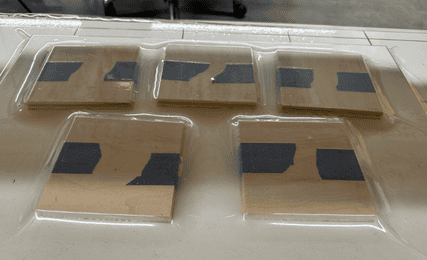
After a day of drying, I pulled the squares out and sanded off excess glue with a belt sander.
The top piece needed a slot for the tissues to come out, so I CNC milled one and then rounded it out with a handheld router. I finally sanded each face of veneer with a handheld sander to ensure the pieces were flush.
Afterwards, I cut each side of each square at a 45-degree angle with a miter saw, then glued and clamped up all the pieces together to form a box.
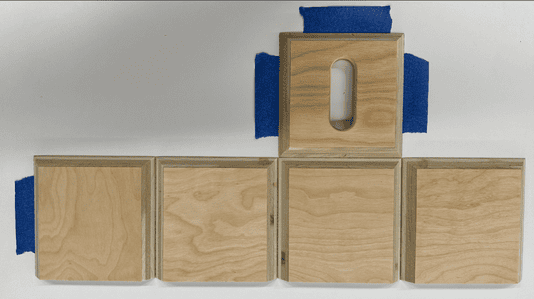
However, it was at this
stage I realized I sanded too much away from the edges, since the edges of each box
were not lining up, creating gaps between the corners. No matter, woodworking is all
about hiding your mistakes! To add my final detailing on the edges of each side, I
miter sawed away the corners and then glued in small edges in dark wood. Finally, I
sanded the whole thing again and applied some finish. I really like how it turned out!
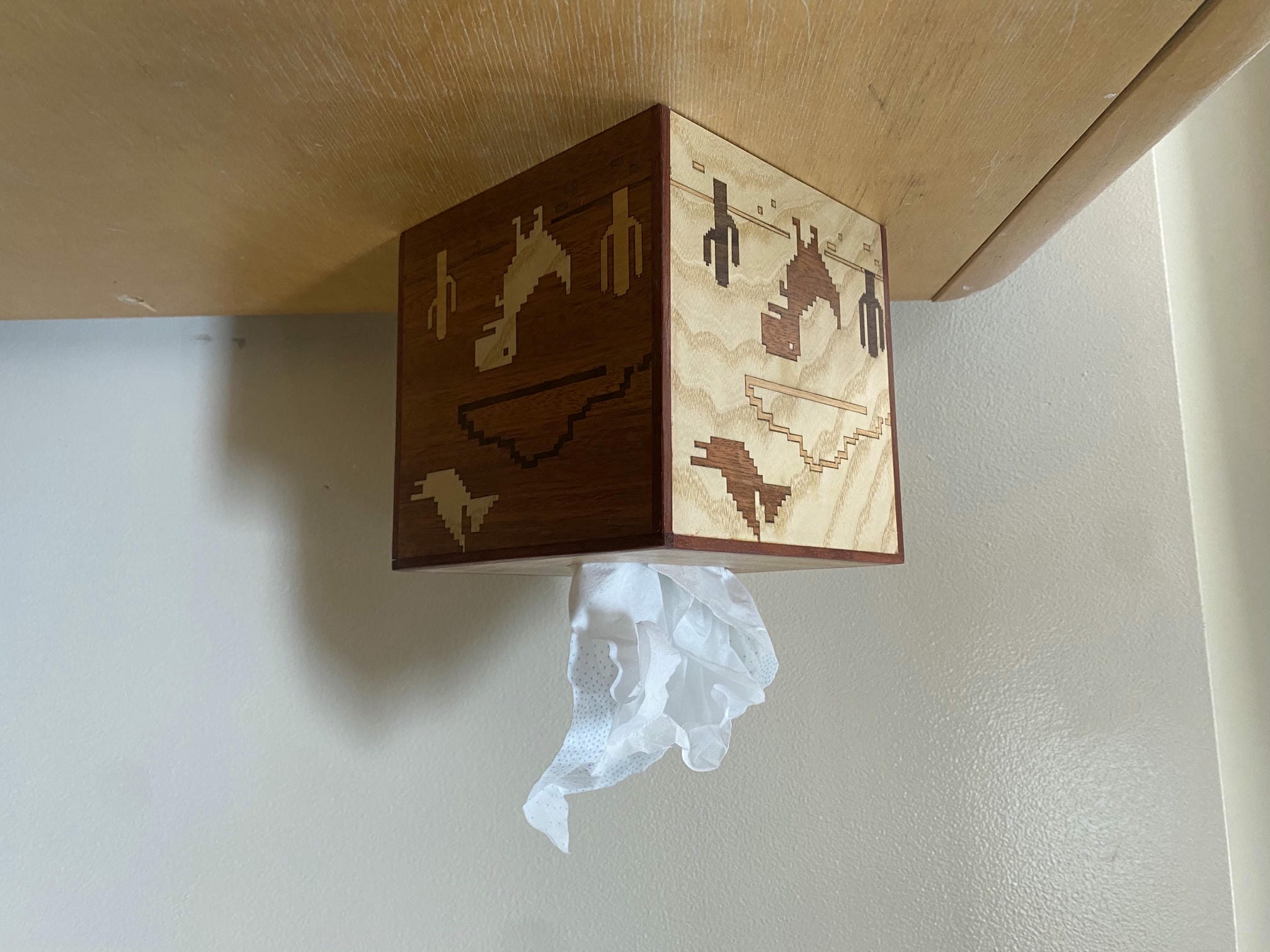
Side note: Woodworking is absolutely fascinating and incredibly dense. There are
so many considerations (grain density, ring size, grain direction, tensile strength, etc.)
which make working with wood different each time, and it truly brings an appreciation in
craftsmanship to all the woodworkers out there. (Oh, and for mass manufacturing. If you
haven’t seen plywood manufacturing
already, you should check it out, because it is insane. You’re literally rolling
apart a tree and then gluing up the parts in different directions to minimize the effects of expansion.)